Flow wrapping machines, also known as horizontal form-fill-and-seal machines, are widely used for packaging a huge variety of consumables that are sold wrapped individually, in multiples or on trays, from chocolate bars to biscuits, and dishwasher tablets to sausages. Mars® bars are an example of a product that is flow wrapped individually and may then be flow wrapped in multiples. Flow wrapping machines incorporate three basic functional sections:
- An infeed section which takes product from the upstream manufacturing process
- A section which forms the bag or wrapper from a continuous reel of film and feeds the product into it
- A crimping section which seals the end of the bag and separates it from the web
These functions are highly dependent on each other and must be synchronised with absolute precision. Generally, products are fed through the machine lengthways in single file separated by a small gap, with the long seal on the back of the bag in line with the axis of travel. Traditionally, the three functional sections of flow wrapping machines have been linked mechanically.
However, this arrangement has many shortcomings, including:
The Issue
- Product changeovers take a long time (typically 30-60 minutes) and require a high degree of skill
- Adjustment of registration to compensate for variations in the film requires a variable-ratio gearbox that is expensive and manual adjustment is coarse
- The bag-making process cannot easily be paused if a product is missing from the infeed queue, or is defective, which results in wastage and inefficiency
- Complex mechanical systems are prone to wear and require high maintenance
The Solution
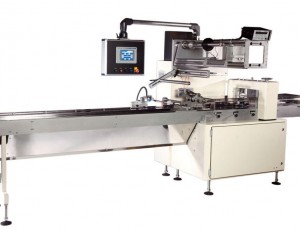
The photograph above has been reproduced with the kind permission of Daco Packaging (UK) Ltd, of Dilton Marsh, Wiltshire.
An elegant solution to these and many other problems is to eliminate the mechanical linkages by driving each motion individually with a servomotor and linking the motors through an intelligent multiaxis controller, which is precisely what I have done for a number of OEMs (original equipment manufacturers) and machine rebuilders.
The products come into the machine (from left) onto a chain conveyor fitted with equispaced pegs that separate each product from the next and drive it forward. The film is held on a reel in the centre section of the machine. It is drawn into the bag forming section by rollers which both pull the film and apply pressure to its edges to form the long (continuous) seal on the back of the bag. It is also here, as the bag is being formed, that the product is fed into it by the peg. The bags then pass between a pair of rollers fitted with radial jaws (usually one or two pairs of jaws) which come together to crimp the film immediately behind the product, which seals the bag and separates it from the one upstream. [The other end of the bag has already been sealed by the crimping operation on the previous bag.] The rotation of the crimp rollers is synchronised with the other motions to ensure that opposing jaws come together in the gaps between the products.
The film is pre-printed with the product information plus a print registration mark. Between the reel and the tooling that forms the bag is a registration sensor, which ensures that the continuous web of film is correctly synchronised with the infeed conveyor, so that the product is inserted into the bag and the end seals are formed in the correct position relative to the printing.
The three axes – product infeed, film feed and crimp rollers – must remain synchronised at all times; for the latest servo-driven machines capable of wrapping 1,000 products per minute or more, this is an extremely demanding application that is only made possible by the use of modern control technology. However, these sophisticated control systems can also perform many other functions that improve performance and reliability, such as continuous registration adjustment on a bag by bag basis, as well as providing additional features such as no product/no bag and no gap/no seal, which would be far more difficult to achieve with traditional mechanical machines.
Another benefit that comes from using computer technology is that controllers can store large numbers of product recipes, each of which may include a large number of variable settings. Recipes can be selected from a menu and called up at the push of a button, making product changeover quick and easy. Operator display screens can also provide a lot of real time information about the process and the latest machines use touch-screens which allow operators to finely adjust settings on the fly. Servo control also greatly simplifies the mechanics, which reduces wear and maintenance and virtually eliminates the need for change-parts with the exception of product-specific tooling. This, combined with the fact that the control systems can be programmed to give highly detailed diagnostic messages and product changeovers can be done in very short time, means that productivity of the machines is greatly increased and downtime reduced. Clearly, full servo control offers enormous benefits.
Tim Oxtoby wrote the software for the servo controller and HMI(human-machine interface) for this flow wrapping machine by Daco Packaging.
My contribution to this packaging machine revolution:
- Helping packaging machinery companies upgrade machines in which the complex motions are linked mechanically to full servo control
- Programming various PLCs and motion coordinators to perform the complex motions smoothly and link them together precisely
- Commissioning servo-controlled flow wrapping machines which achieve performance levels that simply aren’t possible with mechanically-linked machines
- Designing operator interfaces that provide detailed information about the process, allow fine adjustments to be made during operation, provide facilities to create and store large numbers of product recipes, and provide diagnostics messages.
- Mars® is a registered trademark of Mars Incorporated trading in the UK as MasterFoods UK Ltd
Follow Tim!