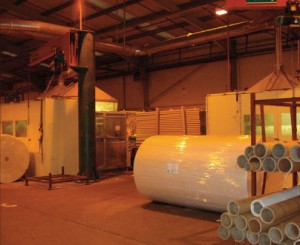
Two of the three machines which take large rolls of paper and convert them into finished products. The machines are housed in acoustic enclosures. The duct for the dust extraction system can be seen in the top of the picture.
Peter Grant Papers, in Telford, is the UK’s largest independent soft tissue manufacturer, converting 15,000 tons of tissue paper per year produced by its Lancaster mill into toilet paper, hand and face towels, and wipes for the healthcare, catering and industrial sectors. At the heart of the company’s environmental policy is the maxim, “Being kind to the environment is at the core of everything we do.” As such, Peter Grant Papers endeavours to reduce waste, increase the use of recycled material and source its pure tissue products from sustainable forests.
In pursuit of this policy, an energy audit at their Telford factory, which operates 24 hours per day, five days per week, revealed a number of areas in which potential savings could be made. One of these was in the dust extraction system supporting three paper converting machines, two of which run continuously whilst the third only runs during the two day shifts and is stopped at night for product change-over and routine maintenance. The dust extraction unit is situated outside the factory. The unit draws air in at the machines at such a velocity that it carries the dust away with it. In the dust separation unit, water mist is sprayed into the air stream to remove the dust, which forms slurry that is recycled. The air is discharged to atmosphere. The fan runs continuously for 120 hours whilst the factory is working.
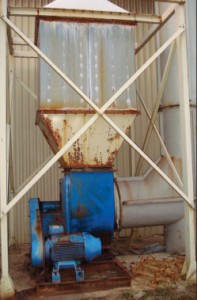
Extraction unit showing the fan and 55kW motor driving it
Simple tests to reduce airflow by introducing a baffle into the duct suggested that extraction would still be effective at a lower airflow rate. However, using baffles to control airflow would only result in small energy savings, because the motor would still be running at full speed. Consequently, the decision was taken to use an inverter to drive the motor.
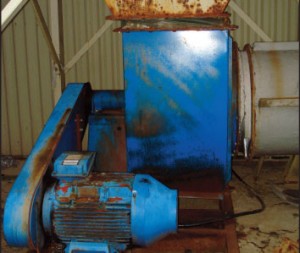
Detail of the dust extraction unit showing the 55kW motor driving the fan through a belt and pulley arrangement.
Before installation of the inverter, the motor was driven directly on line at mains frequency of 50Hz. Tests were carried out over a period, reducing fan speed progressively by reducing inverter output frequency, and observing the effectiveness of the dust extraction. With the exception of one specialist product that is made infrequently, tests demonstrated that fan speed could be reduced to 37Hz (i.e. a 26% speed reduction) whilst still maintaining adequate dust extraction. However, because in fluid handling applications power is proportional to the cube of the speed, the 26% reduction in speed translates to a 60% reduction in motor power. Of course, fan speed can be adjusted when making the one particular product that requires greater airflow for effective dust extraction. The customer has installed a baffle in each leg of the duct, to cut off the airflow through a machine if it is stopped. Relays have been installed in the cabinet, which indicate the number of machines running, and logic in the inverter reduces fan speed proportionately whilst keeping air flow rate through each machine adequate for effective dust extraction. Running continuously at mains frequency, at or near full load, motor power consumed was about 6600 kilowatt-hours per week.
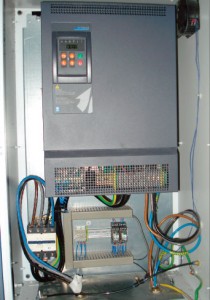
Gefran 55kW inverter mounted in a panel with relays for interfacing it to external controls
At a nominal cost of 4.43 pence/kilowatt-hour, this equated to an expenditure on electricity of: 6600 x £0.0443 = £292.38/week
Reducing operating frequency to 37Hz equates to an expenditure on electricity of: (37/50)3 x 6600 x £0.0443 = £118.48/week
which represents a saving in electricity costs of: £292.38 – £118.48 = £173.90/week
Based on operating for 50 weeks/year, this represents a saving in electricity costs of £8,695 p.a.
This saving gave a payback on the equipment in less than one year. However, there is another, unexpected benefit which hasn’t as of yet been quantified: the reduced airflow means that less heat is lost from the factory, resulting in a further energy saving.
Follow Tim!