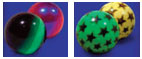
Marballizer and All Star paintballs
This important process enhancement, developed by my company for a leading softgel capsule manufacturer, was subsequently applied in all its facilities worldwide.
Softgel capsules are used for packaging liquid products from bath oil to cod liver oil, and prescription drugs to paint balls. But have you ever wondered how they are made?
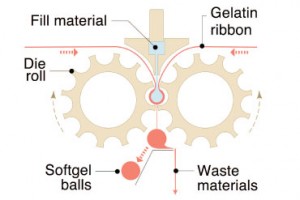
The photographs of RP Scherer paintballs have been reproduced with the kind permission of Pursuit Marketing, Inc. Encapsulation process
Softgel capsules are made and filled on rotary die encapsulation machines. Hot liquid gelatine is continuously cast in two thin wide ribbons, or webs, which set as it cools. The webs pass over rollersguiding them onto a pair of rotating dies having multiple impressions in their cylindrical faces, which come together to form the two halves of the capsules. The impressions are designed to form capsules of a particular size and shape; most are torpedo-shaped or spherical. As the dies rotate, the webs progressively come together until they touch and the gelatine forms little pockets. Metered shots of the liquid are injected through nozzles to fill each pocket, as shown in the diagram. As the faces of the dies meet, it seals the capsules and nips them off from the web, leaving a seam around each capsule. As the die opens, the capsules fall away and the gelatine ‘net’ which remains is re-melted to be used again.
So why, after 70 years of successfully filling capsules using a tried-and-tested process, did this manufacturer come to me for help to improve it? The need to improve the process arose with the increasing use of edible dyes for colouring the gelatine and printing on it, which prevented it from being reused and made it necessary to maximize the yield from the virgin material. In order to do so, the margins between the capsules and the edges of the web were reduced. However, due to a small amount of variability in the web that caused it to wander slightly – which wasn’t a problem when the margins had been wider – the outer capsules occasionally overlapped the edges of the web, resulting in an imperfect seal that leaked and contaminated machine and product. Consequently the machine had to be stopped and cleaned, and the spoiled products scrapped.
The best solution appeared to be to fit automatic web guides to the machines, to continuously adjust the position of the webs going into the rotary die, to ensure correct tracking and alignment at all times. An initial study showed that buying proprietary web guides for every rotary encapsulation machine in all their facilities worldwide would be prohibitively expensive. Consequently, in 1999, my company was awarded a contract to develop a custom-made unit that could be built within the customer’s budget. The first task was to design the web guide itself. We chose a novel approach which comprised a roller over which the web ran, mounted on a pivot that moved it sideways through a small arc, driven by a linear actuator – a stepper motor having a leadscrew through its centre for translating rotary to linear motion. We initially proposed using a pair of sensors to detect the edges of the ribbon, however, its width proved to be so consistent that it soon became obvious that just one sensor could be used for detecting a reference edge. We used a laser-based optical sensor that detected the gelatine despite the fact that it may be clear. Once the final design had been approved, manufacture of the web guide mechanisms was contracted to a specialist precision engineering company.
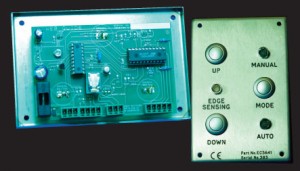
Control box with lid removed
The next task was to develop a suitable controller. An initial investigation into proprietary controllers found that even the most basic PLC when packaged with the other components necessary to drive the stepper motor exceeded the customer’s budget. Consequently, we designed and programmed a bespoke single-board controller around a microprocessor and stepper drive chip, which they packaged in an IP67 housing. Once prototype and pre-production trials had been completed and the design and software validated, we were awarded a contract to manufacture the controllers. So successful is the design that controllers are shipped to the customer’s facilities all over the world where they are connected to the web guide mechanism as a ‘plug and play’ retrofit.
I was given full responsibility for:
- Designing a functional unit which could be made within tight budgetary constraints
- Developing, testing and de-bugging a working prototype and pre-production unit
- Laying out the PCB (printed circuit board) and selecting the components
- Programming the microprocessor for controlling operation of the web guide
- Managing the project to achieve a workable solution within a tight timescale
- Archiving the design information and updating it as components become obsolete
- Manufacturing new controllers in batch sizes typically from ten to one hundred units
- Providing ongoing support for repairing faulty or damaged units as required
Follow Tim!