
Capping machine sitting over the conveyor.
This project for the Japanese life sciences company, Olympus Diagnostica, in Ireland, was to replace an existing machine that was unreliable with a new machine designed and built by for consistently screwing caps onto bottles to a precisely-controlled, repeatable torque. The machine is constructed primarily in stainless steel, with an aluminium alloy superstructure, for use in a clean room. My company was given just three days to install the new machine and get it working before the line had to recommence full-scale production. Bottles of analytical reagent are brought into the machine from the left, indexed into the capping station by the 6-spoke star wheel, then released to the right. They are transported in single file to the capping machine which screws on a cap to a precise torque setting at a rate of up to 20 bottles per minute. A bottle enters the star wheel which indexes 60 degrees to an argon filling station where the gas is injected into the bottle, providing an inert atmosphere which protects the reagent. It then indexes again to position the bottle under the capping head. The star wheel is driven by a Lenze brushless AC servomotor fitted with an in-line reduction gearbox.
A simple two-axis pick-and-place unit takes a cap from the escapement and presents it to the capping head. The pick-and-place unit is powered by oil-free air, to avoid contaminating the clean environment.
The capping head has a collet chuck which grips the cap. The chuck is mounted on a rotating shaft driven by a Lenze brushless AC servomotor, and the whole assembly is mounted on a vertical slide driven by two tandem air cylinders (i.e. air cylinders mounted in line) so that it comes down to a first height to collect the cap then, when the pick-and-place has moved out of the way, it comes down to a second height to screw the cap onto the bottle. The chuck rotates at constant speed as the cap is lowered down onto the bottle, to engage the thread. As the cap bottoms out, the motor continues driving until the required torque is reached, when it stops instantaneously. The chuck incorporates an ejector pin which ensures that the bottle is not picked up by its cap as the head retracts to its home position. The star wheel then indexes to release the bottle back onto the conveyor whilst at the same time bringing the next bottle into the capping station. Capping head and star wheel are driven by Lenze 9321 intelligent servo controllers which have integral PLCs linked to extension I/O (input/output) modules via Lenze’s own version of CANbus. As well as controlling the capping machine itself, the PLCs also control the existing cap feeding system and argon filling system and interlock operation of the capping machine with the line.
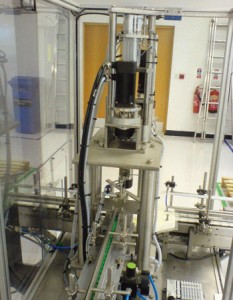
Plastic caps (green) being fed in single file from an existing vibratory bowl feeder along a chute to an escapement then into MCS’s new capping machine.
My company designed and built the capping machine which was then extensively tested ‘on the bench’ in their Telford facility before being delivered to Olympus’s factory for installation. With a tight schedule to meet and just three days during the factory shut-down in which to get the new machine fully integrated into the existing production line, proper management of the project was vital for a successful result. The finished and working machine was handed over on time to the customer’s complete satisfaction. We successfully completed this vital turnkey project for one of the world’s leading life sciences companies on time and within budget.
I was given full responsibility for:
- Designing and building a reliable capping machine to fit into a tightly constrained space
- Integrating the new machine into the existing production line and controlling some of the existing line equipment
- Completing and testing the new machine by a given date, to be ready in time for installation during the factory shutdown. Failure to achieve the required deadline was not an option!
- Installing and commissioning the new machine in a limited period of three days
- Providing all technical and supporting information including operation and maintenance manuals and training Olympus staff
If you have a project critical to your business that you need help with, please contact Tim Oxtoby.
Follow Tim!