When AWE Newtech Limited, a leading manufacturer of resin impregnation machines for electric motors, realised that significant savings could be made in the cost of their flagship machines by introducing distributed control, they approached my company to develop a suitable process control board.
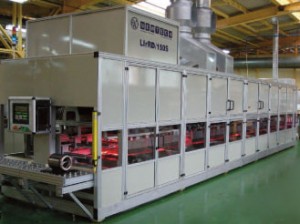
Multi-station Linear Indexing machine for impregnating stator windings, showing a stator at the load/unload station. This machine is one of the largest at 12.5m long
Newtech’s machines are used for impregnating the windings of stators up to IEC 200/NEMA 320 frame (up to 100kg/220lb) with insulating resin. The machines use resins which must be cured at elevated temperature in order to achieve their required working properties. Stators are heated prior to impregnation, to reduce resin viscosity which aids penetration, then heated after impregnation to cure the resin. Heating is provided by electric lamps emitting intense, short wave infrared (SWIR) radiation. Because of the high throughput, raising stator temperature from one process level to the next is done over a number of consecutive heating stations. Typically, machines have between 20 and 60 heating stations in total.
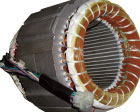
Typical stator
Each heating station incorporates a SWIR lamp module. There are two versions dependent on the size of the largest stator, rated at 6kW and 8kW, having either twelve or sixteen 0.5kW quartz halogen lamps. Each individual lamp is controlled independently, so that it is switched on only if a stator is present directly beneath it and the stator is below its set temperature. Lamps are switched off during indexing, to save energy. In early machines, each lamp was controlled by an individual PLC output, requiring a large number of I/O modules and an enormous amount of wiring between the control cabinet and the lamps. It was eliminating these that resulted in such substantial cost savings. This is where my company
came in …
A large machine could have upward of 1,000 individual 0.5kW lamps, each one switched by a digital output on the PLC, plus 5 or 6 kilometres of wiring between the control cabinet and the lamps. The cost of the PLC I/O modules, plus the labour for making up the wiring looms, was a significant proportion of the total cost.
The densely packed wiring also presented a hazard that could seriously damage the machine in the event of a fire. The process control board developed by MCS, which sits inside each lamp module and controls the lamps, eliminated the I/O and most of the wiring. I worked closely with Newtech’s engineers to develop a detailed functional specification from which he generated the design specifications for the hardware and software. I then briefed a team of highly skilled engineers at their office in the Ukraine, where they specialise in developing bespoke control boards and writing high-level software for a wide range of industrial applications, who produced the prototype board.
The primary function of the board is controlling the lamps, to achieve optimum heating in the stators with most efficient energy usage. The power control side of the board handles real-world currents and voltages, with each lamp taking just over 2A at 230Vac. A fan is fitted to the housing, for cooling the board; despite this, it still operates at 50-60°C.
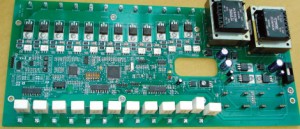
6kW SWIR lamp module with twelve 0.5kW lamps Process control board for the 6kW lamp module shown above
Consequently, I included many military spec components, which are designed to operate continuously at high temperature. The boards are linked via a network to the PLC controlling the machine. Because end users generally specify the make of PLC used in their machines, many of which have their own proprietary network, I included network connections for most of the commonly used PLCs – ProfiBus for Siemens PLCs, DeviceNet for Allen-Bradley PLCs, plus CANOpen and MODBus, as well as an Ethernet connection and RS485 high-speed, multi-drop serial communications link for connection to PC-based controllers.
I also helped Newtech develop the software to implement the network on the PLC. The board was designed to be transparent to the PLC, so that the original PLC code for controlling the lamps could be used without major changes. Because of the processing capacity available, the board has been given far greater functionality, including a soft start feature to extend lamp life, plus lamp life monitoring, and reporting fault conditions such as lamp or fan failure. A second round of developments to further reduce cost included eliminating the interface for the infrared pyrometer used for measuring stator temperature, by conditioning the pyrometer output signal in the processor.
Having proved the prototype, I organised manufacture of boards in batches of 100 pieces. Newtech benefits from substantially lower labour and material costs, easier assembly and improved performance.
Newtech gave me full responsibility for:
- Taking a technical lead and generating the detailed functional specification for the board
- Designing, making, testing, de-bugging and proving the prototype process control board
- Implementing a variety of networks on the board including ProfiBus, DeviceNet, CANOpen and MODBUS allowing connection to most of the commonly used PLCs
- Writing the software for interfacing the board to the PLC and commissioning the machine
- Completing the development project on time and within budget
- Arranging manufacture of the boards in batches of 100 pieces
Follow Tim!