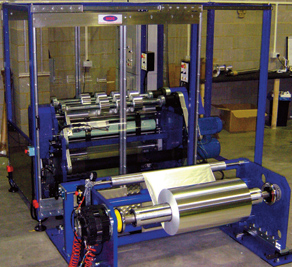
Hybrid centre/surface rewind unit (background) taking foil from a braked unwind unit (foreground)
This project was undertaken for Machinery Development Services Ltd (MDS) in Whitminster, near Gloucester, a leading UK manufacturer of converting machines for paper, foil and film. My company provided the drives and control system for this highly innovative machine, for winding reels of aluminium foil used by hairdressers when colouring hair.
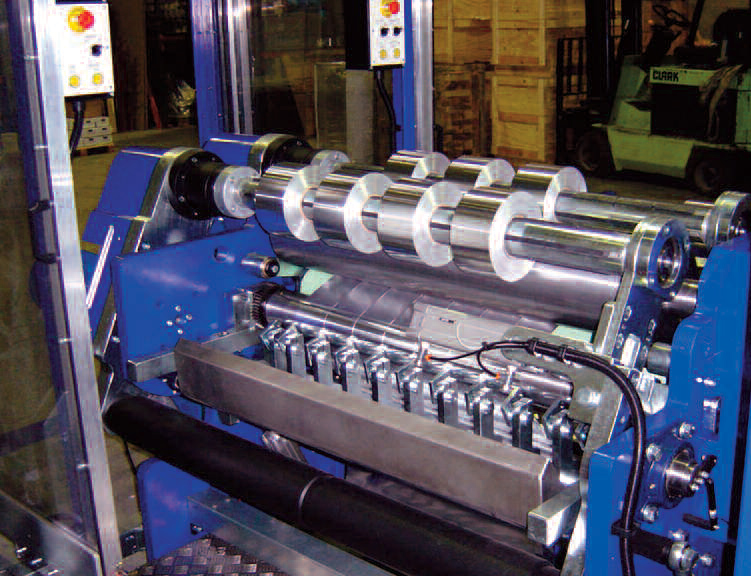
Front view of the rewind unit with seven reels of foil on the two rewind shafts.
The machine converts large rolls of aluminium foil weighing up to 500kg, as supplied from the rolling mill, into small reels that can be conveniently handled by hairdressers who cut lengths from it as required. The foil is unwound from a large reel and slit into strips of the required width before being rewound onto small reels. The roll of foil is mounted on an air mandrel and loaded into the unwind unit. The mandrel incorporates a bladder that is inflated with compressed air, causing it to expand and grip the roll in the bore. The unwind unit supports the mandrel between stub shafts, one of which is fitted with an air brake to control tension in the web. The air pressure operating the brake is controlled by a proportional valve via an E/P (electronic to pressure) converter, allowing the tension to be precisely adjusted and the brake to be applied when the speed demand is zero. The foil is drawn off the roll by the rewind unit.

Rear view of the rewind unit showing the blades mounted on the slitting bar Electrical (above) and pneumatics (below) cabinets with mimic diagrams on the doors showing the key features of the machine.
The foil enters the rewind unit at low level and runs around a roller mounted on load cells which measures the tension, then between the rubber-coated nip roller (pale green) and the main haul-off roller, before being wound onto the rewind shafts. The main roller is driven by a 4kW AC motor with haul-off speed controlled by a Lenze vector inverter up to 250 metres/minute. Each rewind shaft is driven independently by a 1.5kW AC motor with foil tension controlled very precisely by Lenze vector inverters operating in current (torque) mode, to avoid overhauling the unwind unit. Immediately before passing over the nip roll the foil is slit by titanium blades mounted on an air-operated slitting bar. The rewind shafts are mounted on pivoted arms, allowing them to be swung out of the way for loading spools and unloading reels of foil. The arms supporting the rewind shafts are counterbalanced and the reels are kept in contact with the main haul-off roller by air cylinders.
As the effective diameter of the reels increases due to the build-up of foil, the displacement of the arms is measured by linear potentiometers and the torque is continuously adjusted to maintain constant tension. Without such fine control, it would be very difficult to maintain tension precisely using feedback from the load cells alone.
Overall operation of the machine is controlled by a Lenze PLC (programmable logic controller). Status messages are displayed on the HMI (Human-Machine Interface) mounted on the electrical cabinet door. Inverters and HMI are connected to the PLC via a CAN bus network which minimises the amount of wiring between devices. My company provided MDS with the expertise and commitment necessary to ensure this important project was successfully completed and the machine handed over to their customer on time and within budget.
MDS gave me full responsibility for:
- Designing and building the electrical and control system
- Specifying and supplying the AC motors and vector inverter drives
- Wiring and testing the electrical and control circuits
- Writing and debugging the PLC programme for controlling the machine
- Programming the HMI (Human-Machine Interface)
- Commissioning the machine and making it work at MDS’s factory
- Providing all technical material and transferring the technology to MDS
- Commissioning the machine at the end user’s factory
- Training the end user’s staff in the correct use of the machine
Follow Tim!