This project was undertaken for Ridgway Machines Ltd, in Anstey, Leicester, for their customer in India. It was a quantum leap forward in the way complex taping lines are built.
As part of our company remit, we used our expertise and the latest technology to revolutionise the electrical and control system, to achieve a degree of modularity that allows virtually any number of machines to be integrated into a line at the lowest equipment cost, and in the shortest installation and commissioning time.
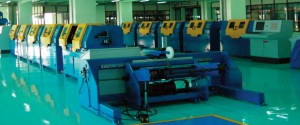
4-machine taping line (H1 to H4, background) and 7-machine bunching line (B1 to B7, foreground)
Line 1 comprises four taping machines (H1 to H4) for wrapping individual conductors to make a single rectangular bar covered with insulating tape. The conductors are taken off a reel at the beginning of the line, drawn through the taping machines by a servo-controlled caterpillar and finally wound onto another reel at the end of the line.
Line 2 comprises seven taping machines (B1 to B7) for bunching three separate bars to make an insulated 3-core cable. The first three machines (B1 to B3) are staggered in height. Each machine is fed from a separate reel and wraps one bar. After B3, the bars are brought together before passing through machines B4 to B7 to be wrapped to form a single cable.
Each taping machine incorporates a Lenze 9300 intelligent servo that synchronises the rotational speed of the taping head with caterpillar speed to achieve the required wrap angle. The 9300 has an integral PLC that controls the machine and monitors the ‘tape low’ and ‘tape break’ sensors, door interlocks, and the pushbuttons on the machine’s control panel. Each machine also has an intelligent touch-screen HMI (human-machine interface) that displays status information about the machine. Each line has a remote operating console containing a Lenze PLC, which ties together the operation of the machines and oversees the safe functioning of the line, plus a PC, screen, keyboard and mouse for entering product data and creating product recipes.
We designed a universal electrical and control system that could be used with these and subsequent lines of machines, which requires the minimum of time and materials for building the panels, wiring the machines, and for installation and commissioning, in order to minimise total cost. We achieved these objectives, producing the ultimate in elegant, efficient and cost-effective solutions.
Key to the modularity of these lines is having a distributed control system using the latest networking technology to simplify communications, as shown here.
We designed a common control module that is used in the caterpillar and in each taping machine. It is based on a Lenze 9300 intelligent servo which has an integral PLC (programmable logic controller) with digital I/O (inputs and outputs) for handling discrete functions (e.g. push buttons,sensors, etc.) and interlocking them with the main motion task. The 9300 controlling each machine, the HMI on each taping machine, the PLC controlling the line and the PC generating the machine settings, which in the case of the bunching line is a total of 17 intelligent devices, are all linked via a CANopen bus. This is a single cable, connecting all machines in a daisy-chain, which allows both simple instructions (e.g. ‘cycle start’) and complex data to be transmitted to a specific machine or to be broadcast to every device on the network. The settings, or recipe, for each product are worked out by the PC using a universal set of calculations that has been devised for all taping applications. These calculations not only determine parameters such as the gear ratio between each individual taping head and the caterpillar, to achieve the required wrap angles, but they also check that none of the rotational speeds and accelerations demanded of each taping head exceeds its safe working limit and, if it does, caterpillar speed is automatically reduced so that all heads work within their safe limit. Having generated the settings, these are transmitted over the CANopen bus to each individual machine.
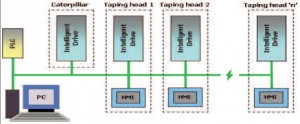
Control system topology
In order to synchronise the taping heads with the caterpillar, the encoder signal from the caterpillar’s drive motor is transmitted from its own 9300 servo controller to the 9300 controlling each taping machine. A major benefit of this topology is that it minimises the wiring within each machine because all links between the logic and motion controllers are internal to the 9300, and because CAN eliminates virtually all of the conventional wiring that would otherwise be necessary between the machines and the PLC. The software is also written to be modular. For instance, it recognises when another machine is added to the line. The software is configured in such a way that the new machine simply needs to be assigned a unique CAN address to become integrated into the control system, which simplifies commissioning.
I was given full responsibility for:
- Designing a modular control system suitable for use on all Ridgway’s taping lines, allowing up to 25 individual machines to be incorporated into a line
- Writing a universal software ‘front-end’ for generating product recipes
- Creating a user-friendly operator interface suitable for any taping line
- Designing and building all electrical power and control panels
- Specifying and supplying the Lenze geared servomotors and 9300 controllers, PLCs, etc.
- Wiring and testing all electrical and control systems
- Implementing the CAN communication network for transferring status information, instructions and complex data between the PC, the PLC controlling the line and individual machines
- Commissioning the machines in Ridgway’s Anstey factory for acceptance on time and in budget
- Providing all technical information and training Ridgway’s staff
Follow Tim!